As governments and corporations promote battery electrification and EVs to achieve their decarbonisation and net-zero commitments, the resultant surge in demand for the minerals to fulfil this growing demand for batteries has global miners scratching their heads.
GROWING OUTPUT WHILE DECARBONISING: A NEW ELECTRIFICATION SOLUTION FOR THE MINING INDUSTRY
Their challenge? How can they dramatically increase output of minerals for batteries whilst meeting their own net-zero and decarbonisation targets, especially when the mining industry today emits at least 68 million tonnes of CO2 per year from its diesel-fuelled haul trucks alone?
The logical solution is for the electrification of the mining industry itself, starting with the biggest contributor of carbon emissions – diesel-powered mobile plants, and more specifically, haul trucks. The largest mining trucks require immense levels of power to traverse the challenging terrain of mine sites – think greater than 2MW continuous peak power to drive the motors (the motors of a typical Tesla 3 are rated around 211kW). Mining trucks also rarely ‘sit still’. They are utilised near-24/7 to meet mine productivity targets and they operate in some of the coldest, hottest, highest and deepest environments across the globe.
In these extreme environments, the batteries on the market today would struggle to continuously deliver the power, energy and lifetime needed for a cost-effective electrification of most mines. So, whilst standard lithium-ion batteries are currently a popular electrification solution for passenger vehicles, improvements in lithium-ion technology are required to achieve this same transition for mining trucks.
Currently, a key concept being explored and trialled for mining, as a step toward electrification, is ‘Trolley Assist’; diesel electric drive haul trucks receive the power to run the electric motors via catenary or overhead electric wire lines, which are constructed on haul roads of suitable geometry and quality. Studies have shown that this can help reduce diesel use by up 90 percent [2], but only for mines that can ‘electrify’ a high percentage of their haul roads. Lithium-ion batteries using niche LTO anode chemistries are today’s best candidate for the tough mining operating conditions, offering high power, fast charge, wide temperature range, long cycle life, excellent safety. However, this is only suitable again for mines which can ‘electrify’ a high percentage of haul roads. This is due to the low energy density of LTO batteries, which limits the haul truck’s battery electric range.
What the mining industry needs to transform its operations are batteries which can match LTO’s high power, fast charge, wide temperature range, long cycle life and excellent safety, but with substantially higher energy density (up to 400Wh/L). At Echion Technologies our unique anode material, XNO® delivers this solution; XNO® is based on Niobium and gives unrivalled performance in fast charging. Cells made with Echion’s material can be designed to safely full fast charge in two to ten minutes and can offer 180 percent of the energy density of the world’s best LTO cells.
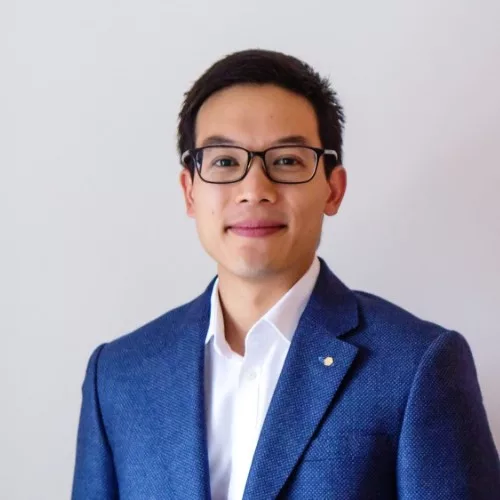
What is needed next is investment in this technology – is the mining industry ready to take the leap?”
Ben Ting, Chief Commercial Officer, Echion Technologies Ltd
Standard graphite anode-based batteries are severely limited in their ability to fast-charge due to fundamental safety and longevity concerns under these conditions. XNO® shares electrochemical behaviours to LTO which guarantees the highest safety and longest cycle life while maintaining best-in-class fast-charging capabilities. As a result, the risk of fire or fumes is reduced to near-zero and mine operators can enjoy a lower total cost of ownership, improving the economics for widespread electrification too. Austmine Charge On Innovation Challenge, Echion’s winning proposal, developed with DB Engineering and Consulting highlight the potential to increase operational efficiencies of haul trucks vs. diesel fleets thanks to the unprecedented design flexibilities unlocked by Echion XNO®. This is a result of XNO®’s ability to safely handle the high power charge delivered using Trolley Assist systems. Maximising dynamic charging, resulted in less or no reliance on stationary charging, and more time to keep moving.
Discussing the matter, Edgardo Pabst Chimenti, Chief of Mine Technology Implementation at Antofagasta Minerals’ Minera Los Pelambres, added: “As mining companies like Antofagasta begin to take action to achieve their net-zero goals, learning about the performance of Echion’s XNO® battery technology through Charge On gives us confidence that a highly competitive solution is right around the corner, helping us to commit to battery technologies as one of our preferred solutions to electrify haul trucks. Battery development is the key factor that will allow us to take the next step, complementing our actual project portfolio which includes trolley systems as one of the cornerstones to start building a greener future.”
It’s clear that the mining industry has the critical role to play in global decarbonisation. Combined with the adoption of on-site renewable energy generation and dynamic charging infrastructure such as trolley assist, XNO® represents the ‘missing piece’ of the mining electrification puzzle. This will enable miners to grow their operations to supply the materials to support widespread battery electrification, whilst reducing the carbon emission of their mines.
What is needed next is investment in this technology – is the mining industry ready to take the leap?
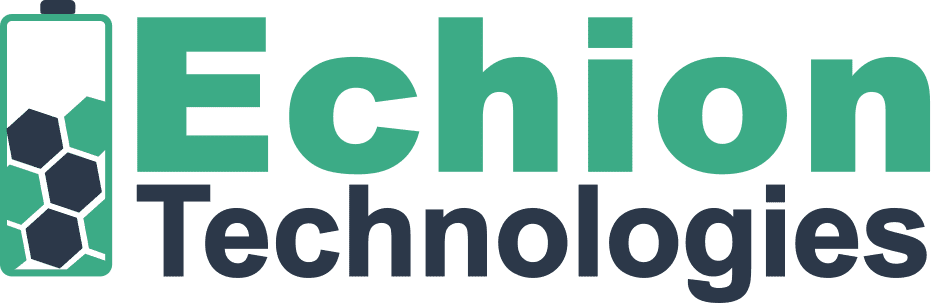
- Raghav Muralidharan, Thomas Kirk, and Thomas Koch Blank, ‘Pulling the Weight of Heavy Truck Decarbonization: Exploring Pathways to Decarbonize Bulk Material Hauling in Mining’, Rocky Mountain Institute, 2019, https://rmi.org/insight/pulling-the-weight-of-heavy-truck-decarbonization
- GlobalData Plc, ‘Development of Electric Mining Vehicles in Surface and Underground Mining, 2022 Update’, April 2022, GlobalData Plc, https://www.globaldata.com/store/report/development-of-electric-vehicles-in-surface-and-underground-mining-market-analysis/