INTRODUCTION
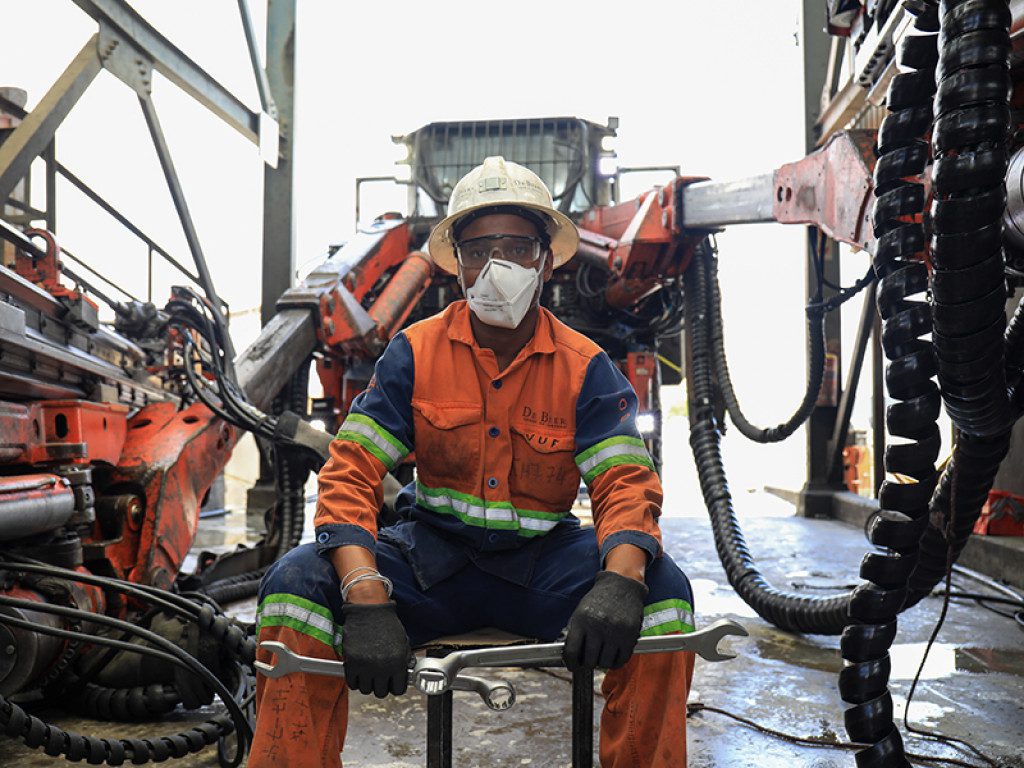
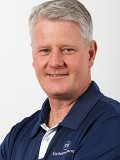
We have a whole series of training programmes outlining where we need to go and how this whole jigsaw puzzle fits together”
Allan Rodel, Project Director, Venetia Underground Project
PIONEERING BRILLIANT SAFETY
Safety is an intrinsic thread in the cultural fabric of De Beers’ VUP, woven through every aspect of operation. This is embodied by the ‘2022 Safety Improvement Action Plan’, which is divided into the following key areas: leadership and governance, cultural and behavioural aspects, training and capacity, technology, risk management, performance, compliance assessment and improvement, contractor management, communication and health and wellness.
Current overall progress stands at 76 percent completion of the annual plan.
The safety and culture plan incorporates the ‘Pioneering Brilliant Safety’ (PBS) framework, which commenced with a roll out in Q3 2021 in partnership with ITD and Safemap, and fulfils an essential role in establishing Venetia Mine as a safe and mature operation.
“We’ve been working with ITD and Safemap for the past 18 months on PBS in our culture change journey. It’s an extremely validating effort in how we’re building the Venetia of tomorrow,” Rodel shares.
“It’s the safety drive I’m most excited about, and through PBS, we continually focus on various leading indicators – what are the things that didn’t happen, could have happened, or how could we have prevented them from happening,” he adds.
Key training programmes are aimed at supervisors and the teams working on the frontline of the mine’s operations, ensuring that all are equipped with the necessary skillset to perform their roles as safely as possible. Going forward, new culture change modules from ITD are set to be implemented across the Venetia Mine site.
“On a daily basis, we drive the culture of identifying things that might result in a negative outcome. You have to look for ways to make safety fresh and engaging.”
One “forward-thinking programme” that Rodel highlights as working particularly well in this respect is ‘Brothers and Sisters Keeper’ – an on-the-spot recognition scheme launched within the past 12 months whereby individuals are incentivised for the correct culture and behaviour and for recognising their peers.
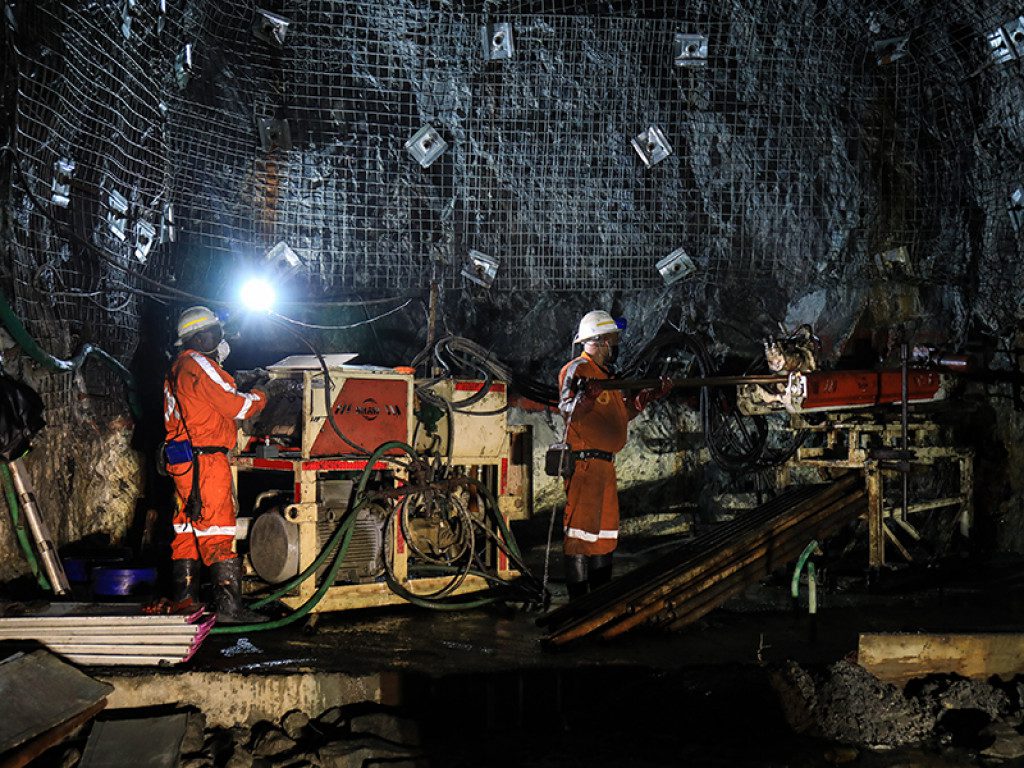
PRIORITISING PEOPLE
It is such initiatives that play a fundamental role in cementing De Beers’ VUP’s stance on prioritising its people and their safety. This is key to both talent attraction and retention, which is essential on an ambitious journey that requires significant recruitment efforts.
“We have pulled out all the stops to make sure we’re attracting the best talent,” comments Rodel, emphasising how the mine is working with different agencies and recruitment partners to entice skilled workers. As an owner-maintained mine, there is an explicit focus on localisation in recruiting people from around Limpopo.
Simultaneously, however, it is equally important to retain those who have a loyal working history at Venetia and train them to work with underground assets.
“We have many employees who have worked for us for over 30 years in our surface operations. It is rewarding to see how many want to keep working for us by transitioning to the underground,” he continues.
At the nexus of this development is the state-of-the-art Skills Development Centre, launched in 2021. A major surface project, the facility is critical in transitioning employees from open pit to underground, whilst also training new employees.
Incorporating the latest technologies, the centre is Mining Qualifications Authority (MQA) certified and boasts video walls, refuge bays, virtual reality capabilities and six simulator training modules, alongside instructor-led classroom facilities, yard training facilities, and dedicated underground skills transfer mining areas for practical experience.
Since 2019, over 130 employees have been successfully transitioned from open pit to underground through rigorous training processes. With a fully developed training management system in place, the facility is in constant evolution to ensure up-to-date skills development for all those involved in the mine – from surface to Top of Mine (TOM) and Bottom of Mine (BOM).
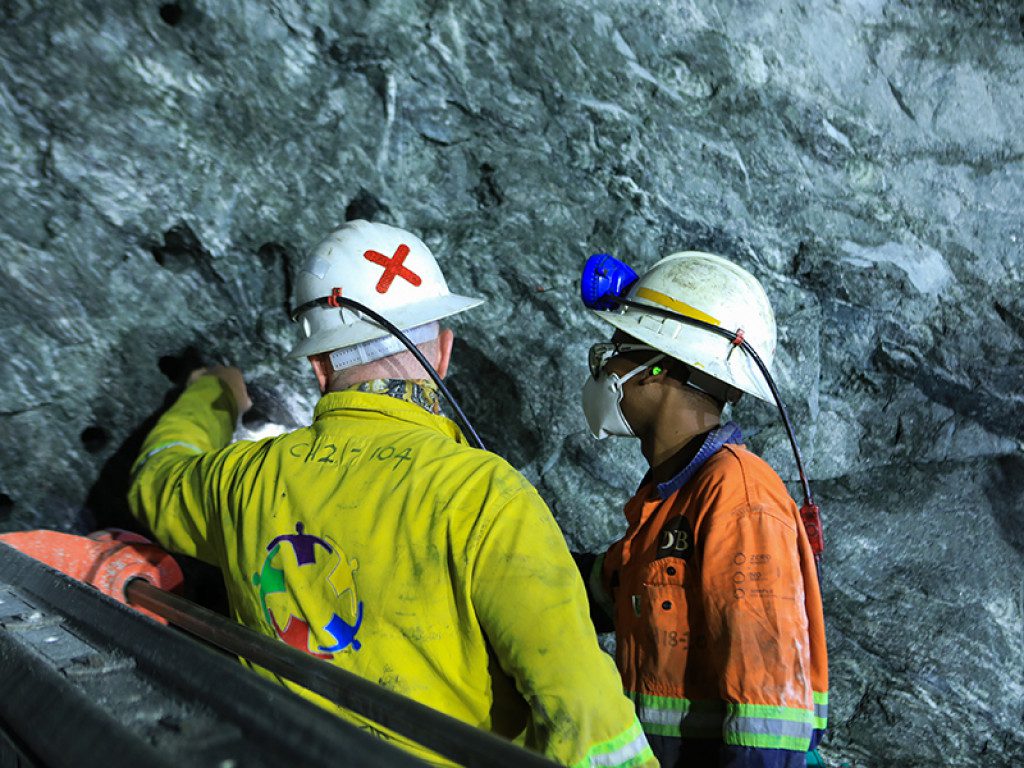
A MINE OF THE FUTURE
Technology is a key ingredient in the change taking place across the site, as VUP follows an ambitious journey of digital transformation. Digitalisation is incorporated throughout VUP’s systems and falls within the overarching vision of establishing VUP as a mine of the future.
“It’s an extremely exciting digital journey that we’re going on,” states Rodel. “Digitalisation is the way we do business, and we have several systems employed to support this vision.”
Crucially, the technological innovation behind this transformation is encouraged to thrive in progress with people transformation, in terms of upskilling and training, to ensure cohesion and collaboration between the two.
This is evidenced by the state-of-the-art Thoroughtec simulators for Sandvik intelligent loaders, trucks, drills and bolters installed in the training centre, and a host of other technological applications concerning skills development. This will only increase in the decade to come, as VUP’s ambitious technological development will see the site aim to become a fully autonomous mining operation by 2027.
The Venetia Underground Technology Development Roadmap outlines that by this time, the underground operation will have established an autonomous mine production system, autonomous navigation/tramming, data analytics, 3D mine visualisation, personnel location tracking, automated asset health monitoring, and a digital operating platform.
Steps towards automation are already underway, as VUP’s first remote-operated loader undergoes safety testing at the facility in Q4 2022.
For Rodel, a series of fundamental questions lie at the core of this “forward-looking lens” regarding the application of technology – how will it affect operations, what does it mean in terms of maintenance, and does it make business sense in light of what VUP is trying to achieve?
“The critical element of technology is that it’s got to make sense and not just implemented for the sake of it. You have to take everyone along with you on the journey of why technology is important – proving that it’s safer, more productive, and making a genuine difference.
“We have a whole series of training programmes outlining where we need to go and how this whole jigsaw puzzle fits together. Everyone must know where they are going and everyone needs to understand the “why”.”
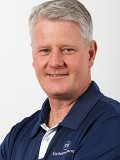
“It will have digitalisation at the core, using data analytics like no other mine, with corporate social investment programmes in place that genuinely make a difference”
Allan Rodel, Project Director, Venetia Underground Project
INVESTING IN THE COMMUNITY
VUP’s emphasis on bringing everyone along with the mine’s future translates not just to its employees, but also the Limpopo communities surrounding its operations, particularly the local suppliers and service providers involved in the project who share in the site’s ambition and vision.
Here, Venetia Mine endeavours to leave a lasting positive impact that will benefit the area long after the mine’s combined open pit and underground lifespan of approximately 60 years.
“The sustainability of our business is critical to us,” introduces Supply Chain Manager Nadine Kok. “We want to ensure that we further develop the skills of our service providers and contribute to the community in a way that means they’re not solely dependent on the mine’s lifespan. There’s a lot of skills development taking place both on and outside of the mine,” says Kok.
One example is the Changing Lives Forever Skills Development Programme. This came to inception after a skills shortage was identified in the labour needed to build accommodation in Musina during the construction and transition phase of the mine. As a result, VUP teamed up with BMH Africa to deliver the necessary skills training to tradespeople on mine accommodation construction projects, with excellent results. Through this project, participants are receiving valuable skills experience, literacy and health and safety training with the appropriate certifications, equipping them with the skills and training to undertake such work anywhere in the country.
Similar initiatives also apply to small businesses, with Kok highlighting local ‘success stories’ such as electrical services contractor Great Nthambe Electrical Services, and Blue Disa – a small civils company run by Mr. Nemakonde – which has grown and evolved alongside the mine over the past decade through its Zimele Business Hub programmes and on the job coaching and mentoring by Venetia Mine employees.
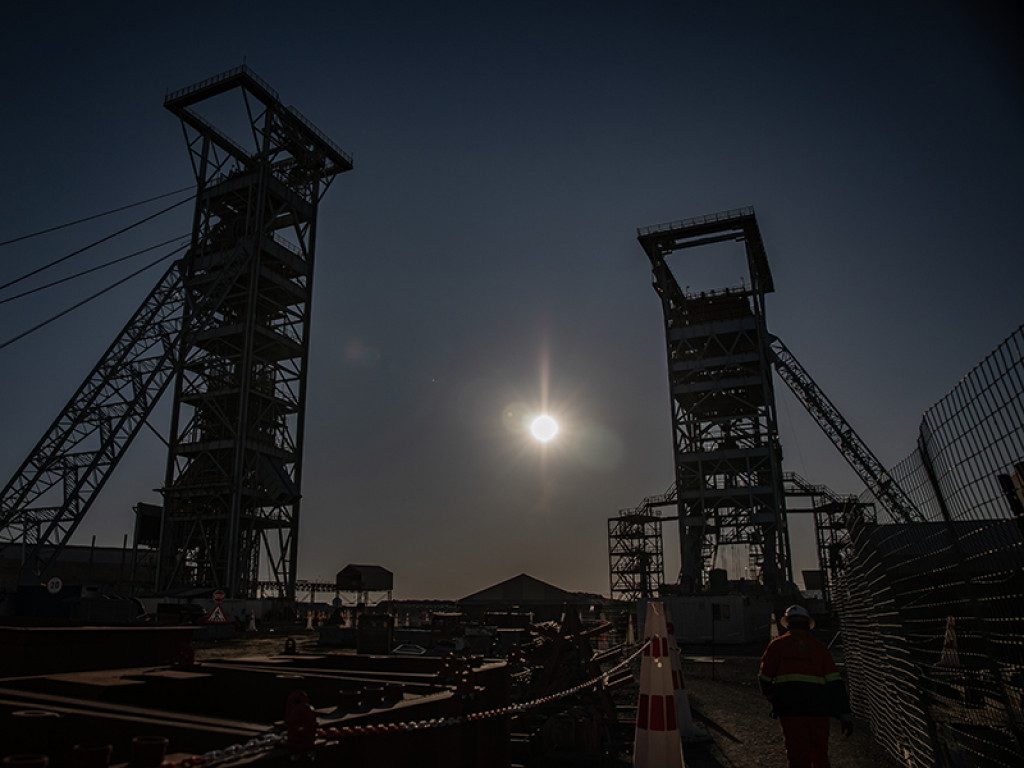
“That programme has been a huge success,” says Kok. “Blue Disa went from being a 100 percent white-owned company, to being fully owned by Mr. Nemakonde. It has since grown from 15 to 60 local employees and has allowed significant business skills development and training on the mine itself,” she elaborates.
Corporate social investment contributions by all the Venetia Mine’s contractors are integral to these efforts as surrounding businesses, and in turn the communities, grow in tandem with the mine.
Returning to the idea of technology and personal development flourishing hand in hand, this is a key focus of De Beers’ partnership with the International Youth Foundation (IYF), where digitised education is making a difference for students enrolled in Technical and Vocational Education and Training (TVET) colleges.
The programme enhances course content and offers valuable work experience opportunities for those studying in institutions near Limpopo and is run in collaboration with the Department of Higher Education and Training (DHET). So far, the scheme has undertaken skills gap analysis, offered enhanced life skills training, established a private sector engagement forum to identify early career opportunities, and has launched online lecture resources.
“We are rewriting the curriculum, adjusting training, providing digitised lectures and equipping students with the necessary life skills to prepare them for a work environment. We are digitising the whole story,” says Kok.
Indeed, earlier this year the programme received the go-ahead for digitised content to be rolled out across 50 colleges in 2022.
“It’s extremely exciting to be part of this journey and to see all the hard work paying off. We look forward to seeing the results at the end of the year,” she concludes.
A PROMISING FUTURE
Drawing to a close, Rodel returns to the vision of a mine of the future that VUP aspires to.
“It’s going to be a mine where people will want to work – a mine that operates digitally in terms of its systems and processes, with the safest and best technology as well as trained, skilled people. It will have digitalisation at the core, using data analytics like no other mine, with corporate social investment programmes in place that genuinely make a difference.”
With all these elements combining, the future for Venetia Mine and the communities surrounding it, is sparkling.