OK TEDI’S SUSTAINABILITY DRIVE
It is estimated that since the beginning of the mine, OTML has contributed around PGK10 billion in assisting the development of economically sustainable local and regional communities within the Western Province. Since 1998, more than PGK3 billion has been invested in decreasing the long-term impact on the river system including the removal of pyrite from the tailings, addition of limestone to waste rock and tailings to maintain alkalinity in the river system and the dredging of sands from the river bed around 100 kilometers downstream of the mine at Bige.
The Ok Tedi mine originally planned to construct both a tailings dam and a waste rock dump to retain much of the mine derived waste during its mine life. However, in 1984, during the construction of the foundation for the tailings dam at Ok Ma, a landslide filled the area. Subsequent state approval was given for an Interim Tailings Storage (ITS) facility which was then developed in a bid to contain tailings at the commencement of operations. Upon the design capacity of the ITS being reached in 1986, further approval by the state was granted for treated tailings to be discharged directly into nearby creeks, eventually flowing into the Ok Tedi and the Fly Rivers.
In 1989, the Northern waste rock dump, that has been developed in the upper reaches of Sulphide Creek, was destroyed by a landslide. Approval was given by the state for OTML to continue using failing waste dumps to the North and South of the pit.
Since then, mine waste was disposed into two tributary systems of the Ok Tedi: Sulphide Creek which joins the Ok Gilor and then the Ok Mabiong before coalescing with the Upper Ok Tedi and Harvey Creek which joins the Ok Mani before it coalesces with the Ok Tedi at Tabubil.
Over the years, the discharge of waste rock and tailings has significantly increased the sediment load of the river. While much of the waste rock consists of coarse material, around 60 percent of it breaks down during transport into finer material in the sand-silt size range. While the gravels aren’t transported beyond the middle reaches of the Ok Tedi, the finer material passes into the Fly River.
The riverine discharge of tailings and waste rock management continues to be the most significant long-term environmental challenge for OTML. This has had adverse environmental impacts on the Ok Tedi and Fly River systems and associated eco-systems, which has subsequently impacted the livelihood and cultural life of the communities who live along the river corridor.
The OTML Environmental team, which consists of environmental scientists and technicians, is responsible for monitoring the past and present impacts of the mine along the 1,000 kilometres downstream riverine system from the mine to the Fly River Delta. This includes maintaining a hydrological network of monitoring stations along the river system, regular field sampling of water, sediment and food, vegetation surveys, data analysis and reporting. The Environmental team collaborates with the community relations team to provide environmental information for the stakeholder consultation.
The resultant heightening of the riverbed over many years has seen an increase in the duration of overbank floodplain inundation.
This flooding resulted in the conversion of parts of the forested floodplain to grassed floodplain in the lower Ok Tedi and the upper reaches of the Middle Fly River system.
Dieback
Vegetation dieback is the result of a substantial build-up of sand in the river channels and during high river flows, over bank deposition of sediments and water floods within the forest in the river’s low-lying floodplains. In addition, communities across the riverbank have had their gardens taken away because of overbank flooding and access to forest resources due to dieback. The extent of forest dieback and changes to grassland is checked every year and reported to the state in the annual report.
Dredging
To help control flooding and dieback, OTML has dredged around 370 metric-tonnes (Mt) of sand from the river at Bige since 1998. The dredging operation removes around 85 percent of the sand that reaches the Bige site located in the lower Ok Tedi preventing it from travelling further downstream. Around 17 metric-tonnes per annum (Mtpa) of sand is removed from the river every year and placed in engineered stockpiles on the East and West Banks of the Ok Tedi River.
The dredging operation at Bige will continue to the end of mine life and this will assist in minimising future physical impacts. The dredging programme has been successful with the bed level of the Lower Ok Tedi dropping since the commencement of dredging and forest dieback declining.
Sulphide Separation
OTML is the only large copper mine globally to separate sulphides from the tailings before the tailings discharge. The residue material following metal product removal is re-treated in the separate Tailings Pyrite Plant flotation plant to extract pyrite prior to disposal.
The pyrite slurry is piped to storage pits on the West Bank of the Ok Tedi River at Bige where it is permanently stored in engineered structures under water with a non-acid forming sediment cover system in order to prevent the oxidation of the sulphides and formation of acid. Once full, the pits are capped with Non-Acid Forming sands dredged from the river as part of the normal sand removal process.
Tailings Disposal
After sulphide recovery from the tailings, the remaining barren sands are disposed of by pumping the material from the processing plant through a pipeline located within the Moscow Tunnel for discharge into tributaries of the Ok Tedi River and eventually into the Fly River.
The tailings are mobilised as a result of the fast-flowing streams and held in suspension until the river profile begins to flatten out at Bige, upstream of the junction within the Fly River.
As the stream velocity slows over a dredged slot in the riverbed, most of the tailings, particularly the coarser particles settle out into the slot. A dredge then pumps the sediments ashore for hydraulic placement into long-term engineered storage stockpiles located on the east and west banks of the Ok Tedi River at Bige.
The reduction in the quantity of pyrite materials flowing down the river has substantially reduced the acid rock drainage risk throughout the river system.
Acid Rock Draining Mitigation
Ok Tedi mine is the only large copper mine in the world to separate sulphides from the tailings before the tailings discharge. The risk of acid rock drainage identified before 2008 because of high sulphur levels and insufficient neutralising capacity in the sediments is now managed with the implementation of the Mine Waste Tailings Project (MWTP).
Since 2008, pyrite and other sulphide minerals are removed from tailings and acid-neutralising limestone added to the mill feed at the primary crusher. The finely ground limestone responds quicker in order to neutralise acidity and is transported with the tailings down the river system. Further, limestone is added to the waste rock dumps to provide neutralising capacity.
Community Mine Continuation Agreement
An integrated compensation and development package are provided to the communities for their economic and social benefit. This is both a moral and legal obligation that OTML must meet, as enforced by legislation passed by the National Government of Papua New Guinea in November 2001.
The Community Mine Continuation Agreement (CMCA) defines the cash compensation, investment and development payments that OTML makes to the 158 communities impacted by the mining operations in return for the license to continue operating the mine until 2025. The communities are grouped into nine regions of over 147,000 people. The nine CMCA regions extend from the mine to the South Fly. These are: Mine Villages, Highway, North Ok Tedi, Lower Ok Tedi, Middle Fly, Suki Fly Gogo, Manawete, Kiwaba and Dudi.
A total of 36 elected community members consist of the CMCA Working Group and attend the delegates meeting along with the government representatives, OTML, churches, women and youth organisations and NGOs. Each region is represented by four community members, including at least one woman. The mine continuation funding is seen by the CMCA Working Group members as a lever for change leading to a self-supporting sustainable future without OTML.
CMCA and Mine Villages Updates
The Community Relations Department (CRD) conducts biennial and annual population and family listing updates for the nine CMCA Trust regions including the six mine villages. The cash payments to the beneficiaries are calculated based on the population of respective regions and directly disbursed to family accounts via the online banking system.
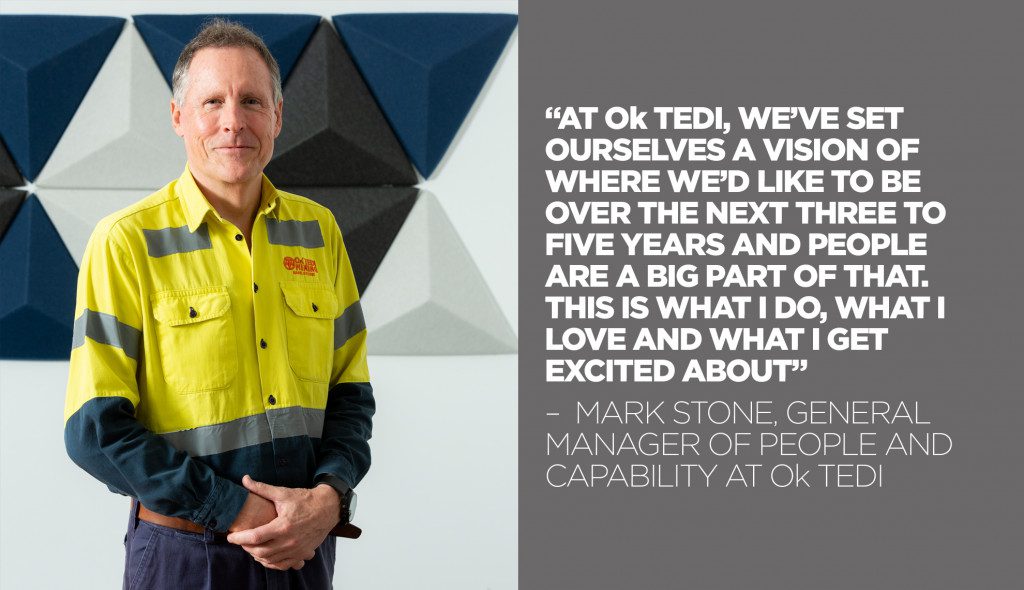