Alireza Oladzadeh, Business Line Service Manager for Gearless Mill Drives at multinational electrical engineering and automation corporation, ABB, discusses the crucial role of long-term service agreements and lifecycle management in gearless mill drive maintenance to sustain the mining and minerals processing industry.
SUPPORTING THE GRIND
Rising exploration costs, volatile market prices, and increasingly remote environments put the mining and minerals processing industry under pressure to adapt.
Meeting these challenges also requires protecting workers health and safety whilst complying with increasingly stringent environmental legislation. Ideally, these issues also require solutions that ensure the efficiency and reliability of equipment with minimal operator intervention.
Against this backdrop of increased demand and squeezed margins is the importance of avoiding downtime. As such, maintaining critical equipment such as gearless mill drives (GMDs) is paramount. However, the complex upkeep of such equipment goes beyond routine check-ups; it necessitates a comprehensive and proactive approach.
Maintenance should not become a priority only when a problem arises. Mines that employ long-term service agreements (LTSAs) can identify issues earlier and course-correct where necessary.
LTSAs blend corrective, preventive, predictive, and prescriptive maintenance strategies with advanced remote diagnostic services. Integrating a comprehensive lifecycle management programme led by a dedicated lifecycle manager facilitates a holistic approach to addressing maintenance issues whilst enhancing safety standards and efficiently managing operational costs.
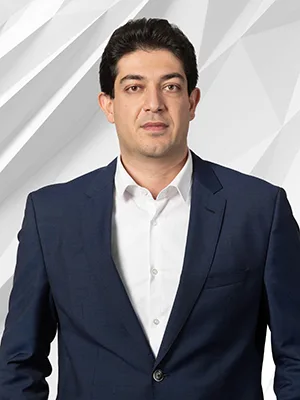
ENHANCED OPRATIONAL RELIABILITY
Offering a gold standard for operational efficiency and sustainability, GMDs are essential to large-scale grinding processes in mining. With their streamlined design eliminating the need for conventional mill drive components like ring-gears, pinions, and gearboxes, GMDs have enhanced operational reliability.
Higher power levels operating with a significant reduction in energy consumption put GMDs at the heart of grinding operations. However, effective maintenance is key to maximising the efficiency and longevity of these components.
LTSAs have emerged as indispensable tools in this regard, providing a structured framework for proactive maintenance strategies. Encompassing a spectrum of maintenance, LTSAs are tailored to mitigate risk and optimise performance.
When implementing LTSAs, mining companies should consider the inclusion of a lifecycle management programme and advanced remote diagnostic applications. These additional agreements cover all levels of maintenance strategies and assure continued functionality and efficiency of GMDs across the board.
Simplifying the maintenance process, LTSAs ensure timely and efficient execution of necessary inspections and repairs. Real-time monitoring of GMD systems allows for early detection of potential issues and prompt resolution before they escalate into costly downtime events. Remote diagnostics also empower operators with actionable insights, ensuring continuous equipment optimisation and operational continuity.
The LTSAs allow experts to remotely monitor GMD systems regularly. This approach significantly reduces the risk of unexpected shutdowns with consistent system checks whilst addressing safety concerns around worker-equipment proximity.
Real-time monitoring and diagnostics of GMD systems are facilitated by digital tools and internet of things (IoT) devices, offering valuable insights into equipment performance and health.
The predictive software calculates potential failures through detailed analysis of historical and real-time data on the GMD’s electrical, mechanical, and thermal parameters to forecast potential failures. This allows for more precise and effective maintenance strategies that adapt to changing conditions and requirements.
Ongoing health assessments allow pre-emptive actions before failures occur, whilst integrating mobile applications enable operators to access status updates and equipment overviews anytime, anywhere.
Instant, remote access to the system, leveraging cloud-based data to identify and address any issues, allows for prompt problem diagnosis and resolution guidance. From support lines and remote troubleshooting to predictive maintenance and condition monitoring, these services are bespoke to the needs of the system.
LIFECYCLE MANAGEMENT
Data is central to corrective, preventive, predictive, and prescriptive maintenance concepts and a lifecycle management programme uses data to successfully integrate all services. The ability to gather and analyse data offers precise visibility into the health of GMD systems, enabling operators to plan or defer maintenance tasks confidently based on condition reports and shifting priorities.
Flexibility and customisation are key components of effective LTSAs as a one-size-fits-all approach is rarely feasible due to varying challenges. Customised solutions enable targeted maintenance strategies that maximise efficiency and cost-effectiveness.
It is also vital that these services evolve with the technology; ABB has worked closely with Boliden at its Aitik mine in Sweden for fourteen years, servicing equipment and systems under four contracts spanning three years each. Continuous adaptation of service requirements to meet the system’s needs helps extend the equipment’s lifecycle whilst reducing associated costs.
Moreover, having experts with GMD field service certifications, familiar with critical equipment intricacies, ensures swift issue resolution. Whether remote or on-site, LTSAs maximise service availability for proactive and reactive support, enhancing asset performance.
EMBRACING THE FUTURE OF TECHNOLOGY
Digitalisation and the integration of IoT are transforming maintenance practices. Employing data analytics and machine learning (ML) to predict equipment failures and issues before they occur enables proactive measures that prevent downtime and extend the lifespan of equipment.
As the mining industry strives to reduce its environmental footprint on the journey to the all-electric mine, maintenance strategies that improve energy efficiency and minimise waste are of utmost importance. LTSAs that integrate these principles not only support sustainability goals but also offer significant cost savings through reduced energy consumption and optimised operational efficiency.