SUSTAINABLE SOLUTIONS INFORMED BY INNOVATION
The company’s roots stretch back more than 100 years to a lush forest near Komatsu City in Ishikawa Prefecture, Japan, which was once home to a copper mine vital to the surrounding community.
Understanding that the world requires equipment to meet the needs of society and the environment today and in the future, Komatsu works to make this as sustainable as possible for generations to come through its manufacturing processes and technologies.
This includes reducing the carbon footprint associated with sourcing and manufacturing through renewable power supplies, remanufacturing components, and strategic sourcing. Technologies such as Tier 4 engines and electric overhead trolley and battery drive systems also improve productivity and reduce greenhouse gas (GHG) emissions during operations.
The company uses numerous digital solutions to further enhance its equipment offering, such as fleet optimisation and health and diagnostics software.
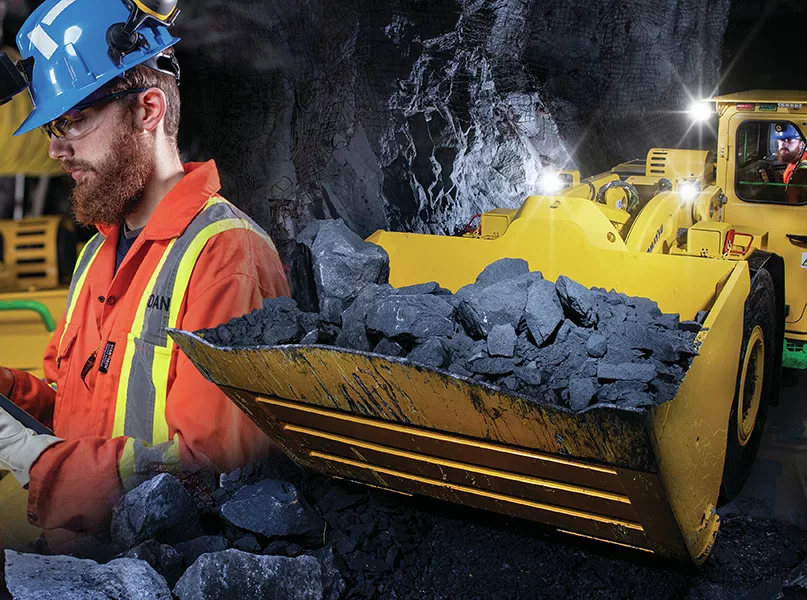
FULL SUITE OF EQUIPMENT
Komatsu offers a full range of surface mining equipment, such as drills, shovels, and trucks, as well as underground hard rock and shaft sinking equipment.
Underground equipment includes load-haul-dump (LHD) machines, dump trucks, jumbo drills, and roof bolters; the latter comprises shaft jumbos, muckers, raise bore strings, stabilisers, and more.
“We offer a full suite of equipment, mining solutions, and services that allow a mine to partner with one brand to deliver the full requirements,” Hollhumer informs us.
“We also have a full service and support offering dependent on customer requirements – this includes parts supply, remanufacturing of components, technical resources, and project and quality management.”
Driven to continuously improve the performance of its equipment, Komatsu focuses on identifying, creating, and delivering value in collaboration with the customers that it services, namely Tier 1 mining houses as well as many other mines, contractors, and a vast construction industry base.
“Some of our customers include Anglo American, Exxaro, Kumba, Assmang, Barrick, FMQ, Foskor, Thungela, Seriti, and Glencore,” he adds.
Komatsu services these customers from its 16 branches and 21 depots across the Southern Africa region, with operations in South Africa, Namibia, Botswana, and
Mozambique, and dealers in Zimbabwe, Madagascar, Mauritius, Malawi, and Zambia.
This is complemented by a parts distribution centre based at Komatsu’s head office in Germiston, Johannesburg, a secondary distribution centre in Kathu that services the Northern Cape region, a component remanufacturing facility in Reman, and a fully-equipped technical training facility that offers basic engineering skills and product-specific training to customers and team members.
“We continue to invest in infrastructure and service facilities to meet the needs of the dynamic environment that we operate in, all aimed at exceeding customer expectations,” Hollhumer shares.
Immersive Technologies, a Komatsu-owned company, also offers simulators for the development of operators and technical staff.
“We offer a full suite of equipment, mining solutions, and services that allow a mine to partner with one brand to deliver the full requirements”
Hermann Hollhumer, General Manager – Mining Operations South Africa, Komatsu
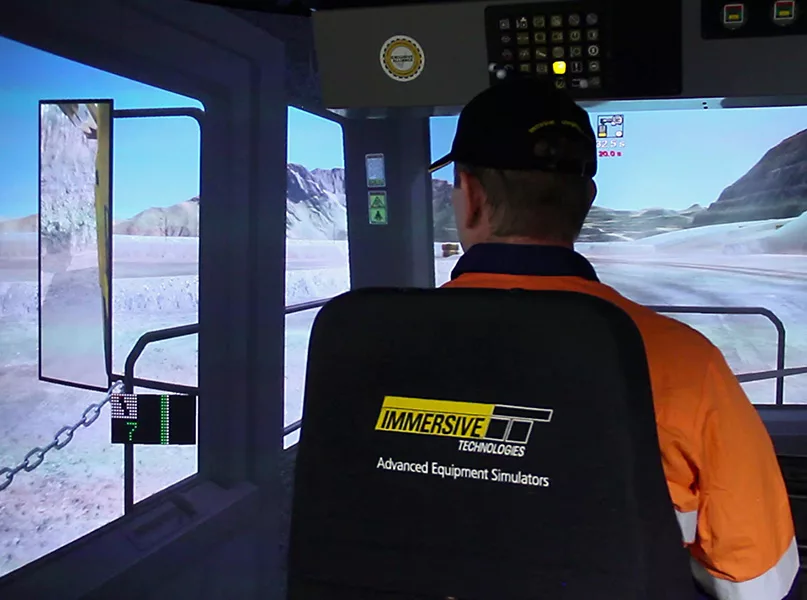
SAFETY COMES FIRST
For all Komatsu employees, SLQDC (safety, law, quality, delivery, cost) represents the order of priority when making decisions.
This order applies to the entire company, including Komatsu’s
offices, production floors, suppliers, and partners.
“We make decisions and act according to the priorities of SLQDC. Safety always comes first, and the order is never mixed or reversed,” emphasises Hollhumer.
“From providing safe products to the overall safety of our automatic operational systems, we persistently utilise the full scope of our innovation capabilities to find ways in which safety is used to maximise the value of our products to our customers.”
Through collaborating with clients, Komatsu develops solutions to mitigate or eliminate hazards in the workplace by integrating DANTOTSU products, services, and solutions to generate a positive cycle to resolve environmental, social, and governance (ESG) issues, including worksite safety.
For example, Komatsu introduced the ICT Bulldozer and ICT Hydraulic Excavator in 2013 and 2014 respectively, which automated the control of blades and buckets. These systems allow less experienced workers to perfectly reproduce the same high-level precision construction work of a skilled worker.
“This has eliminated the need for ancillary workers and guiding processes, thus enabling our customers to make huge savings on rework costs and improving general safety,” Hollhumer explains.
Komatsu’s Autonomous Haulage System (AHS) is another example of a safety innovation that has been implemented in major mines in Australia and Chile by the company, who is also promoting remote controlled operation of the PC7000-11 hydraulic excavator and 100-tonne track dozers for mining sites.
“We look forward to deploying these solutions in Africa. Currently, Komatsu has more than 600 AHS trucks active globally,” he states.
Remote controlled track dozers and hydraulic shovels are additionally offered by Komatsu to complement the transition to autonomous operations. This technology improves the productivity of the equipment and removes operators from higher risk areas.
Immersive simulator technology, meanwhile, offers the ability to practice simulated emergency situations in a safe environment.
“Innovations have improved health and safety when using Komatsu’s products, from doziness detection to collision avoidance interface technology and autonomous operations,” notes Hollhumer.
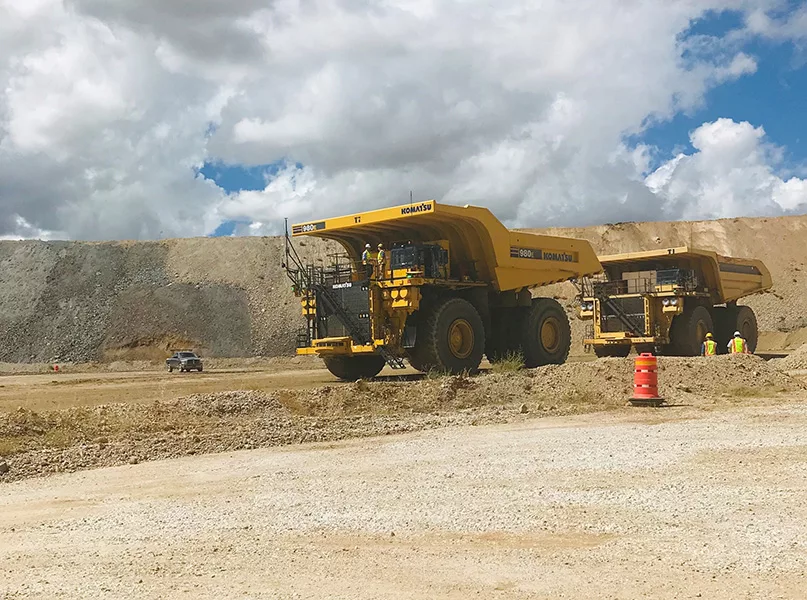
CREATING VALUE
The company is also supplying a 4800XPC electric rope shovel to Anglo American Platinum’s Mogalakwena mine, with delivery planned for April 2024.
Built for tough environments, the 4800XPC delivers consistent uptime, a high cutting force, and is engineered for increased digging power and faster cycle times, utilising the latest mining technology.
“It is the largest shovel in the world, and the first unit in Africa. This is the most energy efficient tool available and has a 20-year lifespan with numerous rebuild and remanufacturing activities to reduce the carbon and raw material footprint,” Hollhumer informs us.
Elsewhere, the company has introduced its underground hard rock fleet options with various market-leading design features, combined with Komatsu’s industry flagship Montabert drifter for improved drilling performance.
Advanced underground digital communication and analytics solutions from Mine Site Technologies (MST) are also offered by Komatsu, alongside the recent launch of an online e-commerce portal, and investment in the growth of the forestry market.
“We recognise the importance of the sustainability of forests and the ecosystem’s importance to the planet,” says Hollhumer.
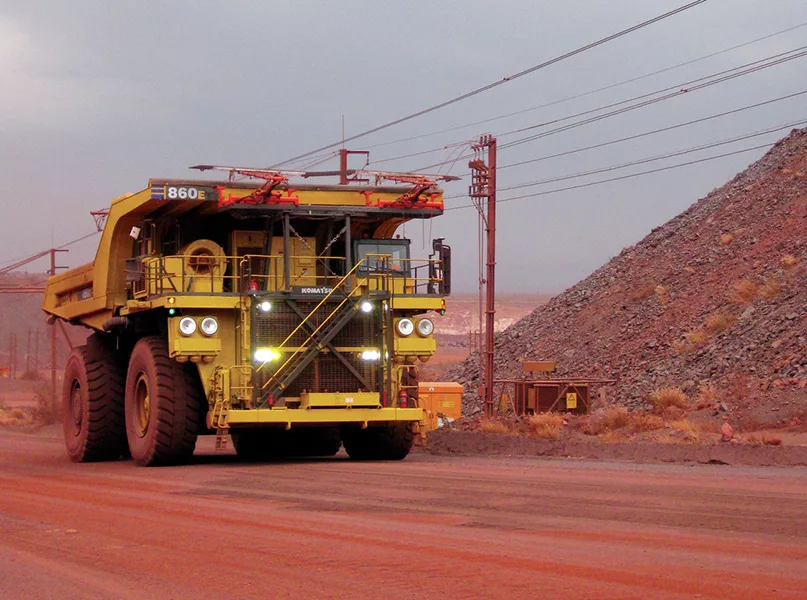
Komatsu equally recognises that people are its greatest asset, as the company seeks to continue to create value and grow in the current era of volatility and uncertainty.
“We believe people are the business, and their contributions in every aspect are invaluable. The ongoing growth of Komatsu will require us to develop human resources with frontline capabilities, built on our four values (ambition, perseverance, collaboration, and authenticity) that support us in acting in accordance with the ‘Komatsu Way’ and fulfilling our purpose,” he outlines.
Just like the good judgment exercised in Komatsu’s corporate management, frontline capabilities need to be honed by accumulating wisdom and tackling new challenges.
“We take great pride in the development of our team members. We aspire to offer technical expertise to meet the demanding requirements of our industry.”
Currently, Komatsu is supporting 100 apprentices and five graduate engineers for its South African operations.
As well as team members, business partners are at the heart of the company’s value proposition to customers. Komatsu partners with local supply and manufacturing businesses to meet the demand of its diverse customer base.
Delivering the operational plans and targets is one of Komatsu’s key priorities for 2024, along with driving towards zero injuries and occupational health incidents, growing the business through improved service and equipment deployment, and harnessing its technology solutions to optimise equipment performance and value delivery to the customer.
“Ultimately, it’s about living our brand promise of creating value together!” concludes Hollhumer.