We speak to executive members of renowned dust management solutions provider and equipment manufacturer, Grydale, about the company’s innovative equipment, sustainable operations, and continuous improvement.
THE MUST FOR DUST COLLECTION
Mines are busy environments that use heavy industrial equipment, often creating dust clouds.
As health and safety experts focus on protecting workers, the demand for dust control solutions is subsequently increasing.
Many industries face harmful dust caused by dangerous minerals such as asbestos and crystalline silica, which can be inhaled during activities like grinding, drilling, cutting, or sanding – this is where Grydale excels.
Established in 2011, the company specialises in engineering, manufacturing, and servicing a range of fixed, mobile, and onboard industrial dust collection equipment.
Grydale’s patented technologies effectively control dust and airborne contaminants in a range of industrial applications, including tunnelling, mining, quarrying, and air quality management in factories.
“Thanks to our proprietary technology, Grydale’s dust collectors have gained a reputation worldwide. They are transforming how dust extraction processes and ventilation design are approached across various industries and projects,” opens Alex de Andrade, CEO of Grydale.
The company distinguishes itself in the market with protected intellectual property that meets the most stringent air quality standards mandated within major projects and has built a strong portfolio for fixed, mobile, and onboard dust solutions.
“This provides a significant and sustainable competitive advantage within the global dust control market,” adds General Manager of Sales, Adam Wallace.
The company is further looking to invest in independent air quality monitoring technology, providing certified evidence of air quality and filtration efficiencies as it maintains an unwavering commitment to continuous improvement and innovation to keep ahead of global air quality regulations.
“Our patented technology has allowed us to deliver solutions to dust challenges that were previously not possible. This, combined with our passionate team, supplier parts selection, and manufacturing and quality processes, are the attributes that truly set us apart in the market.
“We select and test the best available parts for our machines to have maximum uptime and this attests to the support we get from our longstanding suppliers on a 24-hour basis,” de Andrade prides.
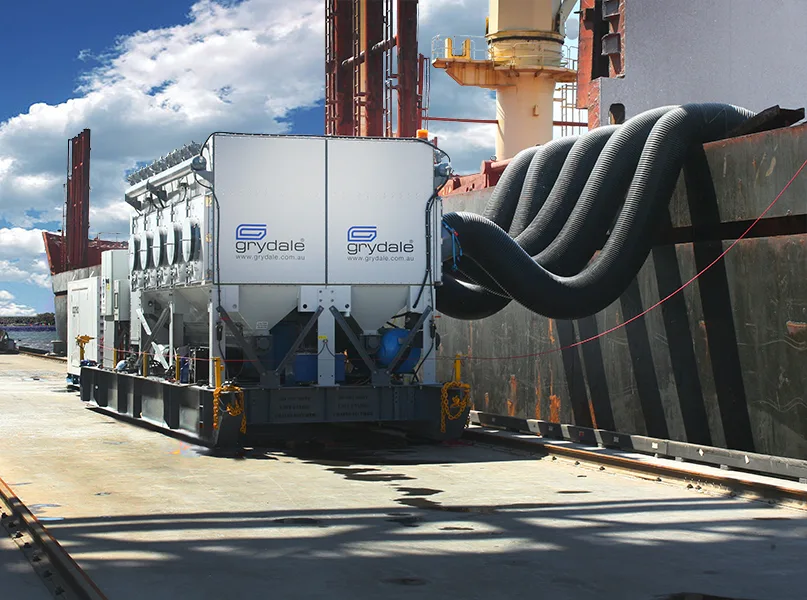
STRINGENT SAFETY STANDARDS
The risk of dust-related diseases increases with exposure levels, therefore, workplace health and safety legislation now requires strict dust management and diesel particulate matter (DPM) control through permissible exposure limits (PEL) and workplace exposure limits (WEL).
Regulations are periodically reviewed and updated to reflect current scientific evidence linking exposure to disease.
“Our dedicated engineers and artisans are committed to continuous improvement, with a strong focus on eliminating waste and minimising safety risks,” urges de Andrade.
Silicosis is the most common occupational lung disease worldwide and is often referred to as the modern-day asbestos.
“By adopting Grydale’s advanced dust control methods, companies can protect their workers, comply with regulations, and enhance overall operational efficiency,” de Andrade suggests.
Grydale is rapidly building a robust reputation for driving up industry standards with its safe and efficient dust extractors as accountability and compliance regulations relating to health and safety within the construction industry are continually tightened.
The extremely high safety standards set by the company extend to its own team, who are willing to enact the exact level of caution for co-workers, family, and friends, as well as the next generation.
“With our dedication to ISO 14001 compliance, we handle the washing of our machines and returned rental units with the utmost care. The same way we protect the operators servicing our machines from any exposure, we do likewise for the environment and neighbours,” de Andrade assures.
Grydale believes there is always a safer and cleaner way of doing any task, accordingly, it retains all washed water and slurry in contained bunded areas and recycling tanks, disposing of the contents through certified waste handling companies.
“There is no compromise for protecting the most amazing part of the country around us in the Moreton Bay region,” de Andrade affirms.
“Our intellectual property is patent-protected and manufactured with the highest quality control standards AND the best componentry for each application”
Alex de Andrade, CEO, Grydale
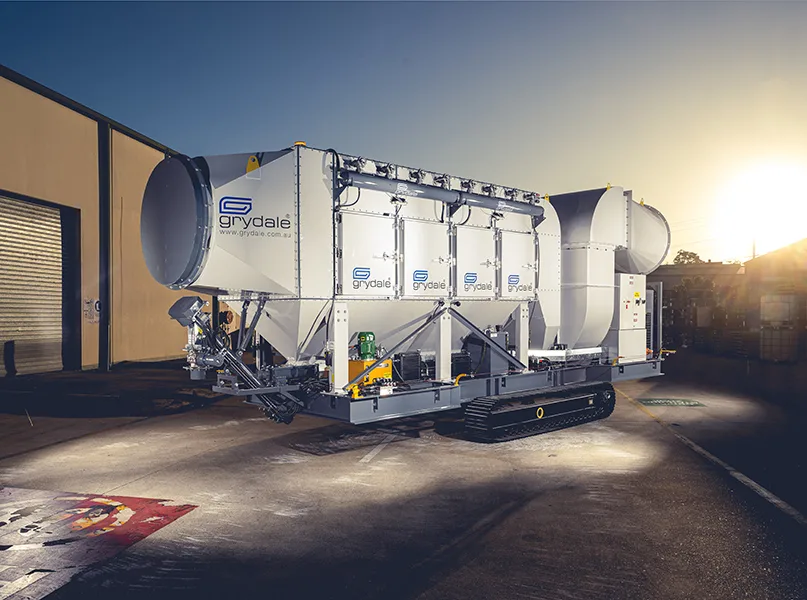
A TEAM UNITED BY DEDICATION
Employees are drawn to Grydale’s strong culture and ethical principles, which prioritise safety by eliminating risks and providing a safe working environment.
The company currently has staff across Australia, the US, and Canada, with service contractors and spare parts also in the UK, New Zealand, and Saudi Arabia. It also has plans to expand its consignment and field support within the UAE, Hong Kong, and Europe.
“Our dedicated field service technicians work closely with clients to provide routine and preventative maintenance schedules, ensuring maximum machine uptime and optimising our solutions’ operational efficiency,” shares Jamie Baskett, General Manager of Field Service.
“We understand that dust control solutions are often critical parts of operations, so our service team works closely with our warehouse and procurement teams to ensure stock of essential spare parts and service items is available to our customer base when required as part of our world-class customer and service support.”
To enable efficient and timely operations, Grydale’s team utilises advanced, state-of-the-art equipment.
“Our in-house team of engineers and designers use advanced 5D building information modelling (BIM) and computer-aided design (CAD) with material property metadata, integrated into our enterprise resource planning (ERP) procurement system, to create bills of materials and drawings for production,” de Andrade expands.
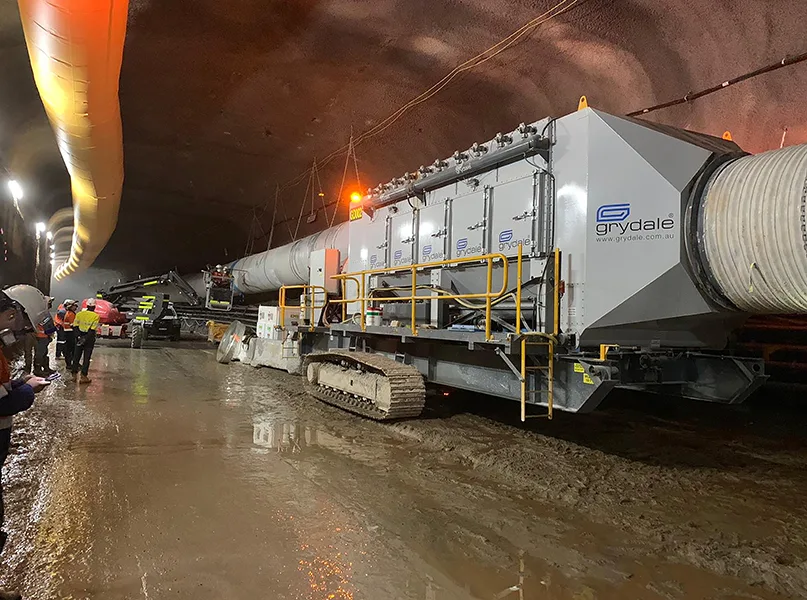
As Grydale transitions from a 15-year-old family-owned business to a shareholder-owned entity with an investment for steady long-term growth, some manufacturing workflow changes have been necessary to meet customer demands and lift the service deliverables in full and on time.
Under challenging product specifications, the founding team and owner moved the company forward to a formidable original equipment manufacturer (OEM) brand that has proven itself in the market.
“Our shift to a multi-national structure aims to build a foundation for scalable growth whilst retaining agility. As a result, the focus moves from completing individual projects on schedule to a global model prioritising quality, consistency, and delivery on time,” acknowledges de Andrade.
Each machine must fundamentally be a replica of the one before it so that simultaneous, consistent technical support is possible on all machines worldwide.
“When customers request spare parts or performance support, we must ensure the as-built status and accuracy of the parts book, manuals, maintenance procedures, and troubleshooting guides cater for global supply equivalent parts but sourced locally.
“Our business model ensures that field service teams or local contractors are available in-country, maintaining strong face-to-face interactions and relationships, with routine monthly inspections of our rental fleet,” de Andrade notes.
Grydale is committed to developing people skills and succession as it grows, creating more opportunities for its employees.
In addition to apprenticeship and graduate programmes, Grydale offers advanced leadership training and sponsored tertiary education support for key roles like technical degrees and Master of Business Administration (MBA) programmes to improve service quality through training and retention.
“We are testing productivity and efficiency for four-day roster work weeks in certain divisions, empowering a culture of completing the job correctly the first time and enabling us to try new rosters and lifestyle approaches,” de Andrade delights.
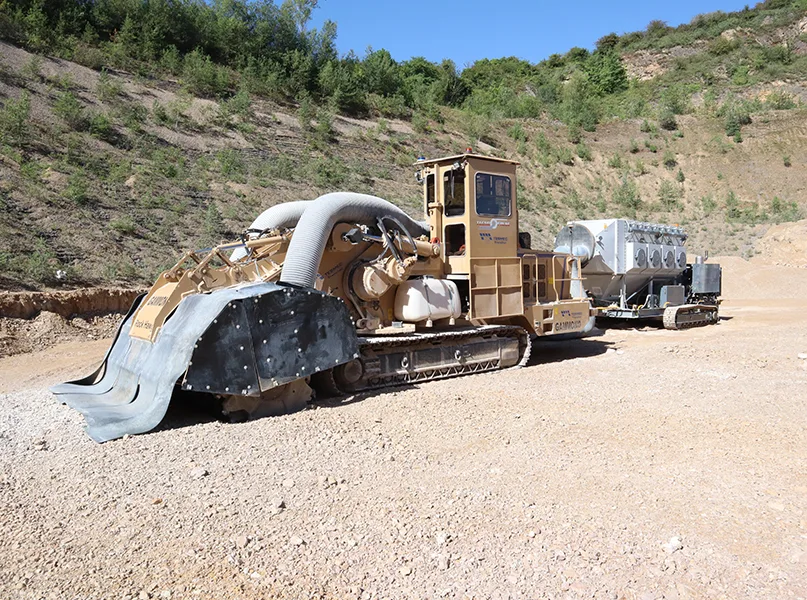
DESIGNED TO LEAVE COMPETITORS IN THE DUST
Grydale’s team ensures complete control over the design and manufacturing of dust control solutions, exceeding performance, safety, and environmental standards to create leading products in the market.
“Our approach involves customers in the process, which is beneficial. Engaging a multi-disciplined team in the design has often led to new ideas and allowed us to push the boundaries of what is possible,” Wallace insights.
The team aims to understand the holistic dust control challenge by communicating with customers, visiting sites, exchanging documents, and evaluating key factors such as dust type, particle size, air volume, and industrial processes.
“Input from stakeholders, including project, plant, and operations managers, health and safety officers, and procurement teams, is essential. Their insights help us define project goals and find effective solutions, making every team member a vital part of the process,” Wallace emphasises.
Production begins when designs are finalised, with the company using a triple ISO certification platform, namely ISO 9001 Quality, 14001 Environment and 45001 Safety accredited quality control process.
Utilising LEAN principles and semi-automation, the company produces both standard and customised equipment, achieving a 94 percent on-time delivery rate.
“Our fabrication facility has its own world-class laser cutting, bending, and pressing machines, which allow us to be in control of quality and reduce manufacturing lead times,” de Andrade elaborates.
In-process inspections and tests are performed at each stage of the manufacturing cycle, ensuring adherence to specifications and reliable final designs.
“After installation, performance is monitored when equipment is operating and feedback is sought from site personnel to optimise the solution further and inform future improvements, fostering a cycle of continuous innovation,” outlines Andy Greenslade, COO.
Grydale also has a fleet of rental equipment, which has opened up new market opportunities where there are short-term or temporary dust control requirements. Rental equipment has also supported major infrastructure projects with out-of-sequence and subcontracted temporary works.
“There should be no reason why an employer isn’t trying out our gear for a one-to-three-month rental trial and obtaining feedback from their work crew as to how much safer they felt the air quality was when they were alongside a Grydale machine,” acclaims de Andrade.

TUNNELLING TO TRIUMPH
Grydale developed a patented, track-mounted mobile dust collector initially for underground use, enhancing efficiency in tunnel construction and transforming ventilation and excavation methods.
Dust collector supply contracts in Australia quickly followed, with major contracts for Melbourne Metro, WestConnex Stage 3A and 3B.
In 2021, over 100 units operated underground for ventilation and dust control during tunnel excavation. Recently, they have also been used in major projects such as City Rail Link (CRL) in Auckland, Sydney Metro Central Station, HS2 in the UK, Neom in Saudi Arabia, the Western Sydney Airport Tunnel, M6 in Sydney, and Northeast Link in Melbourne.
Grydale has additionally worked on significant projects within the mining, quarrying, abrasive blasting, and ship loading industries.
The Melbourne Metro Tunnel project posed significant challenges for the ventilation design, such as space and noise constraints. However, Grydale overcame these by using Ventsim Design 5.0 to simulate ventilation, airflows, pressures, heat, gases, radon, fire, and other critical factors.
The company’s approach was to implement an alternative ventilation design, using a full extract ventilation model, with dust collectors operating on the surface during the excavation of underground stations. This led to the design and manufacture of the largest airflow mobile dust collector available on the market – 60m3/s, 125,000 cubic feet per minute (CFM).
Elsewhere, Australia’s largest public transport project Sydney Metro, in the country’s most populous city, is expanding its network and increasing the frequency of trains. The upgrade of Central Station incorporated Grydale’s JMS-50-MES dust collector for ventilation and dust control during excavation works.
CRL, meanwhile, is New Zealand’s first underground rail line and largest transport infrastructure project.
Grydale designed a ventilation system for Karangahape Road, one of the main streets in the central business district (CBD) of Auckland, that uses negative pressure to draw air through the tunnel and expel it via ducting to the JMS-60-MES dust collector.
“We are also supplying units for the North-East Link tunnelling project in Victoria, including the JMS-60-MES with 1,000-volt harmonics and the JMS-30-MHT dust collectors. These solutions offer significant advantages for our customers and enhance our market position,” Wallace adds.
Grydale dust collectors have also provided effective dust control during major mine shutdown works, including demolition and relining of calciners and furnaces.
The use of dust collectors has helped to provide a clean and safe working environment for contractors and generate operational efficiencies. This approach is now being cited as industry best practice.
“Partnering with Grydale offers clients advantages in navigating stringent environmental regulations and enhances their reputation and business opportunities”
Andy Greenslade, COO, Grydale
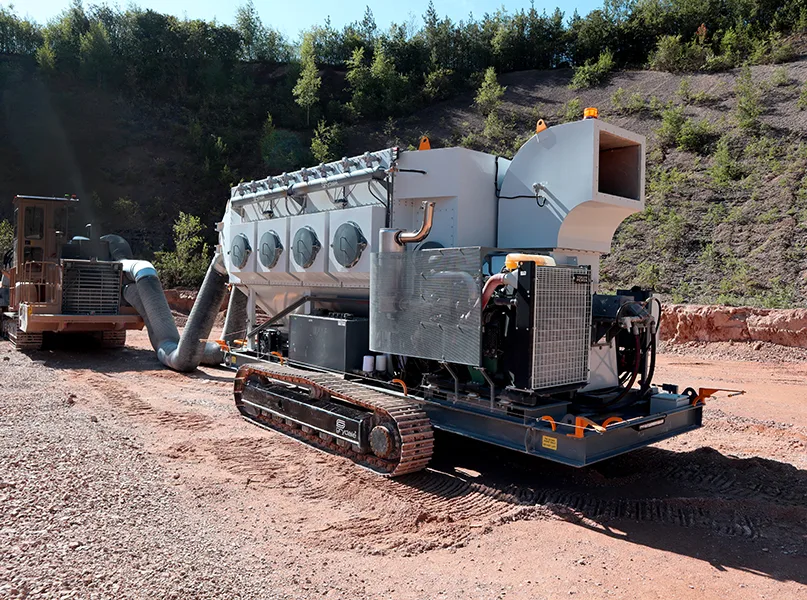
NEW OPPORTUNITIES
Currently, Grydale has 16 units working in the Neom Tunnels in Saudi Arabia and is finalising a distributor agreement to provide additional local support for existing units operating and future sales into the UAE.
“This partnership will provide us with local sales, service, and support staff in a key growth region, where dust control regulations are rising in response to growing health, safety, and environmental concerns,” de Andrade assures.
The global tunnel construction market will continue to be a major focus for Grydale, complemented by its work in the mining sector in Australia and North America.
“To support our expanding customer base in Western Australia, we are selecting a location for a field service centre in the region. Facilities will hold consignment stock and inventory to provide spare parts and rental equipment to better service the region,” de Andrade continues.
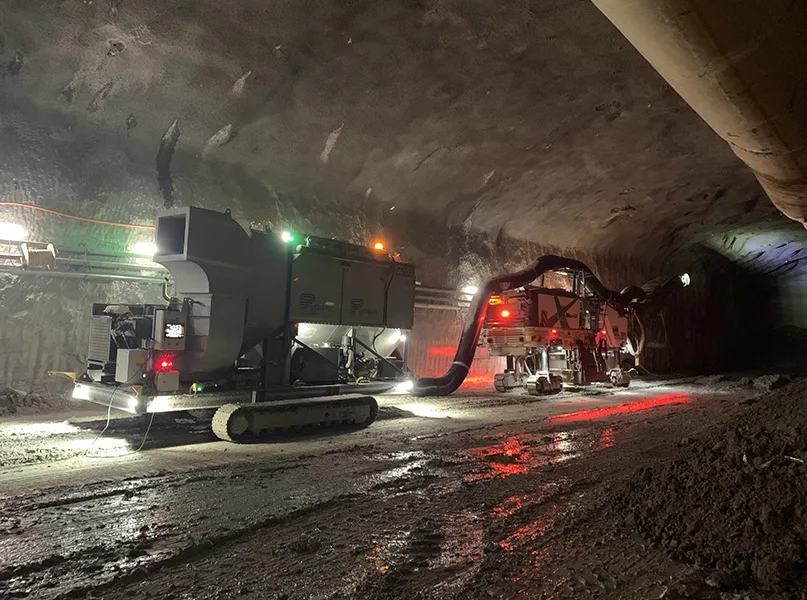
A SOLID STRATEGY FOR SUCCESS
In 2023, Grydale focused on diversifying its equipment for deeper mining applications by upgrading its CAD system and design database.
This allows machinery, such as laser cutting and bending equipment, to operate directly from CAD files, improving change management efficiency.
Grydale has also introduced a Remote Monitoring Service that provides access to key data on machines worldwide. This service helps customers and our team to ensure equipment is operating efficiently and optimised to maximise dust collection efficiency and machine up-time.
“At the same time, customers can use these parameters and reports for predictive maintenance, finding faults, and keeping machines at optimal performance. In mid-2025, we will offer hands-on onboarding for operators using our equipment for the first time,” de Andrade reveals.
The second area of innovation is onboard dust control systems, where a kit is designed, manufactured, and tested by Grydale in collaboration with the customer or the OEM.
“The on-board systems reduce the need for an additional dust control unit to operate onsite,” de Andrade sets out.
The company is working with four partners on repeat business for skid steers, and surface miners and large track trenchers.
“The onboard dust control solution for skid steers to manage dust when sweeping areas with silica sands is a game-changer,” declares de Andrade.
Alongside a two-year strategy to build a solid foundation for future growth, Grydale’s long-term plan is to expand and support loyal customers in North America and Western Australia.
“We have successfully increased production throughput capacity at world-class quality standards and have been acknowledged with our triple ISO accreditation for those efforts.
“Our goal is to raise awareness of health and safety concerning dust and harmful respirable levels. By working with key industry sectors, we aim to create safer work environments, to allow people to return home safely and enjoy their jobs.
GRYDALE PARTNERS

