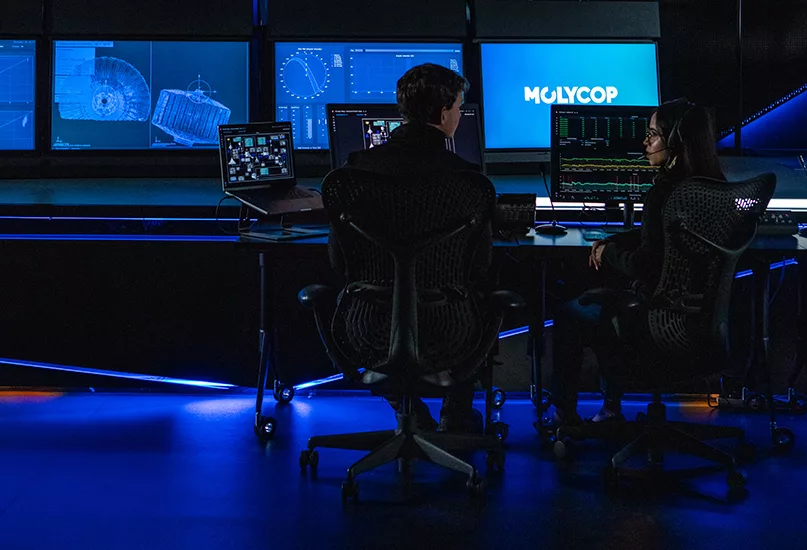
“We are focused on helping our customers increase throughput and maximise recovery with our portfolio of products and services across milling, flotation, leaching, process optimisation, and training.”
AT THE CUTTING EDGE OF INNOVATION
“Our unique selling point is one that places us beyond direct comparison. We’re incredibly proud that Molycop’s strength is not one or two things in isolation; it is the sum of our parts”
Jim Anderson, CEO of Molycop
BRIEF HISTORY OF MOLYCOP
- 1917: First site established under Commonwealth Steel in Waratah, New South Wales, Australia
- 1930s: Sheffield Steel invented and patented the first heat-treated grinding media alloyed with molybdenum and copper, giving rise to the Molycop brand name
- 1961: Sheffield Steel began its international expansion into Chile
- 1998: Commonwealth Steel expanded into Indonesia
- 2002: International plants were acquired by Scaw Metals Group
- 2007-2010: The foundation of the business as it operates today emerged, with OneSteel acquiring Commonwealth Steel through its purchase of Smorgon Steel and then acquiring the North and South American grinding media operations of Scaw Metals
- 2011: Under OneSteel ownership, all the business’ grinding media manufacturing facilities merged into a common Molycop organisation, creating the largest grinding media company in the world
- 2017: Acquired by American Industrial Partners (AIP), Molycop adopted a global business model continuously improving its fulfilment and service innovation
- 2018 – 2019: The company embarked on further geographic expansions acquiring Donhad (Australia) and Metso Sabo and expanding its reach into Africa and the Middle East.
- 2020 – 2023: Molycop has developed a comprehensive instrumentation and process optimisation offering through the acquisition of Mill Trakka sensor technology, Digital Control Lab (“Millslicer”) and Process IQ.
PROCESS OPTIMISATION SOLUTIONS
As is expected in any major industry that plays a large part in driving economic growth, the mining industry is continually evolving and facing new challenges, including pertinent subjects such as declining head grades, skillset challenges, and developing local communities.
However, technology is an enabler that allows the industry to meet these challenges head-on. “Molycop has been the leader in our industry for over 100 years, and it’s only a natural progression and is expected we take a leadership position in working with our customers to help them solve these issues through the use of more advanced technology,” comments Anderson.
Operating with the desire for constant evolution and standing at the forefront of the industry, Molycop has established a new business portfolio under the strength and reputation of the company brand to emphasise its commitment to sustainability and innovation with the extensive range of products and services at the customer’s disposal.
For example, Molycop’s innovation team has significant research projects underway with leading universities in materials science and comminution. With a major initiative such as the development of the Molycop Digital Engine, projects such as these underpin the future product and service developments within the company.
“These new capabilities truly build on Molycop’s rich history, paving the way for a future that’s better when we create it together,” expands Anderson.
Under one strong identity, Molycop prides itself on its holistic portfolio offered to customers, continuously raising the bar for progress, accessibility, and reliability.
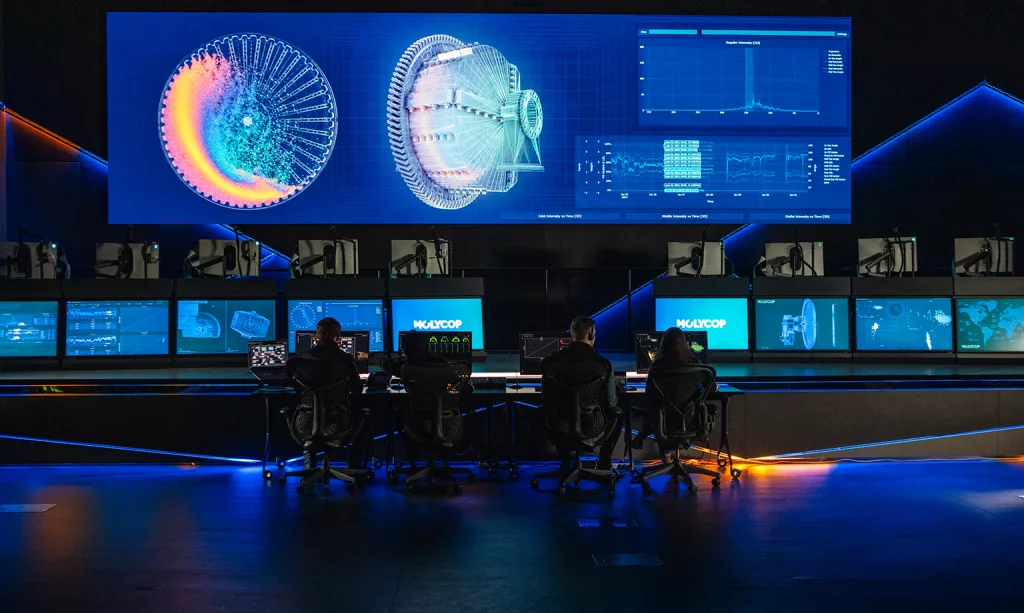
ARTIFICIAL INTELLIGENCE AND MACHINE LEARNING
Molycop has placed a focus on moving beyond the accuracy and flexibility limitations of traditional mineral processing analytical techniques, which were traditionally based on empirical models and rule-based systems, to opportunities in new powerful tools for data analysis, prediction, and optimisation.
“Around the world, we are seeing a positive impact in the way Molycop’s customers are benefitting from artificial intelligence (AI) and machine learning (ML),” notes Anderson, “including real-time predictions and the optimisation of mineral processing operations.”
One such example of this positive impact that has been developed to predict the behaviour and optimise the performance of comminution circuits is the Molycop Digital Engine, an advanced intelligence computational framework specifically tailored for optimising crusher-to-floatation circuits. Additionally, the Digital Engine is integrated with Molycop’s mill monitoring system, including shell and mill sensor data with main operating variables.
Always leading the way for progress and innovation, Molycop’s Dr. Yousef Mohammadi will present a paper, eMolycop Digital Engine: Machine Learning-accelerated SAG Mill Optimisation, at SAG 2023 in Vancouver. And Mukesh Singh Bisht, who is undertaking his PhD co-supervised by Molycop at Sydney University, will present a poster display titled “Heterarchical Comminution Model for Rotary Mills”.
Advanced instrumentation, data capture and visualisation, and data integration with AI and advanced analytics overlay are all aspects that are crucial to the future of mining and are supported by Molycop’s global team of qualified experts.
GLOBAL SUSTAINABILITY
As a company with an expansive global reach, Molycop works to positively impact people, support local communities, and minimise our environmental footprint through every aspect of the company.
Committed to the pursuit of greater sustainability in a manner that allows for superior efficiency of resources and achieves the highest standard of environmental performance, Molycop is dedicated to creating lasting benefits that are responsible, transparent, and respectful to the rights of all.
Polymer Injection Technology (PIT) is a groundbreaking initiative Molycop, in collaboration with the University of New South Wales (UNSW), is spearheading to reshape Electric Arc Furnace (EAF) steel manufacturing by partially substituting traditional coke with rubber from tyres and other sources.
“The benefits are many; however, the clear environmental stewardship is a focus area for us. Beyond financial advantages, PIT significantly reduces carbon emissions by minimising electrical energy consumption,” expands Anderson.
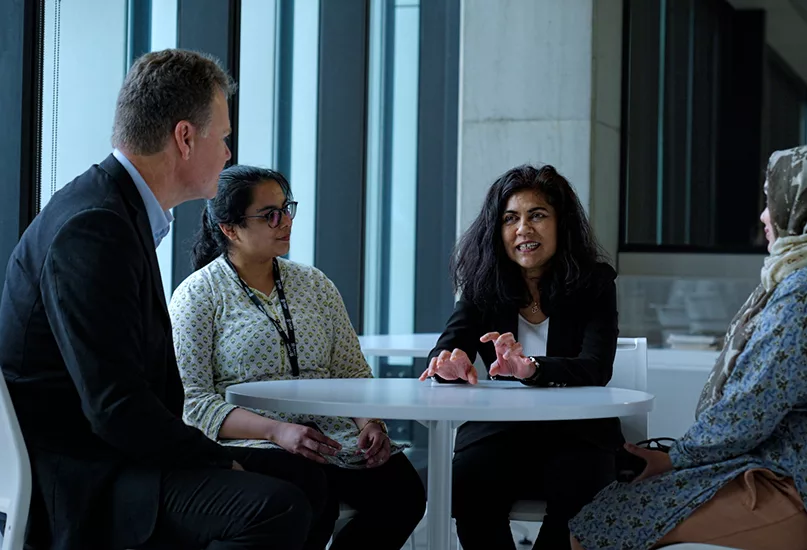