OVERHAULING HAUL TRUCK OPERATIONS
Q&A WITH DAN SWALLOW, PARTNERSHIPS MANAGER, ECHION TECHNOLOGIES
As the economics of the industry rapidly change, the upfront investment in the right electrification technology needs to become less of a barrier to adoption across the industry.
For the moment, while the upfront costs of developing new electric machinery and haul trucks are higher than those associated with diesel equipment, in the long term, electrified equipment can be lighter, smaller, and simpler to operate than their internal combustion counterparts.
They will also have a lower total cost of ownership and lower maintenance costs throughout their lifecycle. Furthermore, without the exhaust and diesel particulate emissions, there will be less need for ventilation and cooling within underground mining shafts, which will save a significant cost. Once these savings are factored in, pursuing electrification presents itself as an attractive business case for the industry.
What are some of the challenges of electrifying the mining haul truck fleets?
DS: Introducing new, operationally unproven technology to a new industry is never simple. Battery-operated mining machines must be adapted to work in the world’s harshest environments and hot, humid underground conditions, while delivering the same reliability as the incumbents powered by diesel.
The largest mining trucks require immense levels of power to traverse the challenging terrain of mine sites, regularly requiring more than two megawatts (MW) of continuous peak power to drive the motors.
Mining trucks also rarely ‘sit still’ and demand continuous high-power input from their engines. In these extreme environments, the batteries on the market today would struggle to continuously deliver the power and energy needed for the widespread, cost-effective, and safe electrification of most mines.
Trolley Assist allows hybrid diesel-electric drive haul trucks to receive the power to run their electric motors via a catenary or overhead electric wire lines, which are constructed on haul roads of suitable geometry and quality.
Studies have shown that this can help reduce diesel use by up to 90 percent, but this concept only works for mines that can ‘electrify’ a high percentage of their haul roads and reconfigure the infrastructure cost-effectively and quickly when these haul roads change. Most designs today don’t achieve this, meaning this isn’t a feasible solution for many mines across the world.
It is important to note that technologies from other sectors, such as rail, could improve the feasibility of such systems, but again, some of these concepts are yet to be proven operationally in a mining environment.
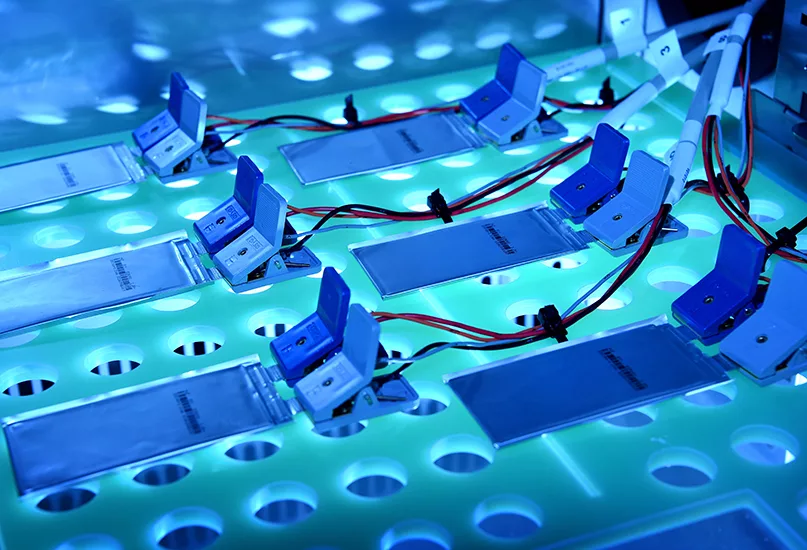
Why can’t current battery technologies meet the needs of these haul truck operations?
DS: Standard lithium-ion batteries used in the majority of passenger electric vehicles (EVs) are not capable of meeting the needs of heavy-duty vehicles. Such batteries use graphite-based anode materials, which offer high energy densities but are restricted to lower charge rates and a limited state of charge window.
Furthermore, graphite anode batteries aren’t well suited to operating in typical mining conditions due to fundamental safety and longevity concerns when operated in high-rate and high-temperature environments for extended periods of time.
Lithium Titanate Oxide (LTO) batteries can charge fast, offer high power density, and are one of the safest and longest-lasting chemistries available, but lack the energy density to make them viable for a full range of mining vehicles.
Novel anode materials have the potential to remove many of the limitations of current battery technologies, as they can significantly and simultaneously improve charge time, cycle life, energy density, and safety.
Echion’s unique anode material, XNO®, can play a significant role in solving this limiting factor in heavy-duty and off-highway EVs. XNO® is based on niobium, which delivers unrivalled performance in fast charging.
Lithium-ion cells made with our anode material can safely and fully charge in two to 10 minutes, increasing vehicle uptime and offering up to 180 percent of the energy density of fast-charging chemistries such as LTO.
XNO® shares similar electrochemical behaviours to LTO in that it guarantees the highest safety and longest cycle life whilst maintaining fast-charging capabilities that perform better than graphite anode materials in heavy-duty machinery.
Research conducted by Ghent University also revealed that XNO® has a carbon footprint 2.5 times lower than LTO at cell level. As a result, mine operators can enjoy high safety, lower total cost of ownership, and an improved economics and emissions profile for their fleet operations.
What is stopping the mining industry from wide-scale adoption?
DS: We recently collaborated with miners in the Austmine Charge On Innovation Challenge, where our winning proposal, developed with DB Engineering and Consulting, highlighted the potential to increase operational efficiencies of haul trucks versus diesel fleets thanks to the new design flexibilities unlocked by XNO®.
This is a result of XNO®’s ability to safely handle the high-power charge delivered using a modular Trolley Assist system, maximising dynamic charging and resulting in less or no reliance on stationary charging. This ultimately means more time to keep vehicles, and profits, moving.
By engaging with miners, we identified that one of the major barriers to adoption is the industry doesn’t feel informed enough to pick an electrification solution and invest in it. Battery technologies and electric power solutions, such as hydrogen fuel cells, are changing all the time, so the industry’s apprehension about throwing itself behind a solution when something more effective might come along is understandable.
However, this indecision doesn’t make the need any less urgent, and collaboration and engagement are the only solutions. The chemical innovators and solution manufacturers can invent novel technologies and customise their existing technology and know-how quickly, but without collaboration with the operators to really understand the issues and work through these together in trials, the most effective solution for each operator is in danger of being passed by.
New battery chemistries are more adept to the high productivity and low total cost of ownership needs that mining has, but greater input and engagement are required from the mining industry.
In the meantime, innovators like Echion are ready to help miners understand the process of going from chemistry to battery systems to help them assess the risks, uncertainties, and opportunities.
The mining industry understands better than anyone the challenges of the supply chain for battery minerals. What does the supply chain for niobium, and batteries containing niobium, look like?
DS: Another positive of niobium-based materials is that niobium is neither rare nor scarce and doesn’t require intensive mining practices to access it.
At Echion, we have established a multi-year manufacturing partnership with CBMM, the world’s leading supplier of niobium products and technology. The partnership has seen the construction of a new 2,000 tonne (t) per year facility in Brazil, which will enable us to supply our ultra-safe, fast-charging, and long-life XNO® battery anode material at scale.
The facility in Brazil, due to open this year, will have the capacity to supply XNO® anode materials at a scale equivalent to one gigawatt hour (GWh) of battery cell production. This uniquely positions us as the first in the market to guarantee the commercial supply of niobium-based battery anode oxides at a scale capable of supporting global electrification targets, particularly for industrial EVs.