Rob Moffitt, President of Mining, Minerals, and Metals at Schneider Electric, explores how the industry can transition to sustainable practices by using an alternative power supply.
HARNESSING ELECTRIFICATION TO REDUCE MINING’S CARBON FOOTPRINT
Mining could be one of the most vital sectors for the global energy transition. If the world is to fully embrace renewable energy and reach net zero for greenhouse gas (GHG) emissions, mining output for the critical minerals that underpin these technologies will need to increase six-fold by 2040.
According to the International Energy Agency (IEA), over the past few years, demand for lithium has tripled, nickel has risen by 40 percent, and cobalt has jumped by 70 percent due to increased requests for new renewable energy technologies. However, while we are mining critical resources for the energy transition, the process is responsible for as much as seven percent of global CO2 emissions, with diesel-powered equipment still accounting for up to 80 percent of a mine’s direct emissions.
As pressure mounts on the mining industry to transition to net zero, electrification has become a strategic imperative not only for environmental stewardship but also for the long-term resilience and competitiveness of mining operations on a global scale. Electrification is key to reshaping the mining sector by addressing its environmental impact, enhancing operational efficiency, and providing a roadmap for sustainable practices that will be crucial for the industry’s future.
THE BUSINESS CASE FOR MINING ELECTRIFICATION
Fuelling mining processes, equipment, and power generation with low-carbon or decarbonised electricity is critical to reducing the industry’s carbon footprint, particularly when an estimated 28,000 large mine-hauling trucks remain in operation worldwide, which emit more than 68 million tonnes (t) of CO2 annually – the equivalent generated by more than 8.5 million homes annually.
To date, electrification projects have primarily focused on mining equipment. The Borden mine in Ontario, Canada, has proven that equipment electrification to reduce emissions is achievable without sacrificing performance. For example, Newmont converted its entire underground truck fleet from diesel-powered to battery-powered fuel. As well as reducing CO2 emissions, this transformation has improved air quality, removed expensive internal combustion engine maintenance, and reduced noise pollution.
However, electrification will also significantly impact operational efficiency, particularly regarding underground mining. Electric engines operate at around 90 percent compared to just 30 percent for diesel engines, while the remainder of the engine emits heat into the ambient air. Switching to electric engines could safely decrease ventilation by 30 percent, while removing the build-up of harmful gases and providing and circulating a source of clean air to miners deep underground.
Since ventilation can account for up to 50 percent of the total energy consumption, mitigating the necessity to power fans at such a high rate would significantly reduce operational costs.
Moreover, electrification can significantly improve safety and working conditions for mine workers, not least because electric vehicles (EVs) and machinery reduce exposure to diesel fumes, improving air quality. Reducing noise pollution also creates a safer and more comfortable working environment. These benefits are not just about compliance or operational improvements – they are crucial for attracting and retaining talent in an industry that is becoming increasingly difficult to appeal to skilled workers.
Electrification is a strategic investment that can lead to substantial returns through improved productivity, operational flexibility, and a safer working environment. These advantages will prove paramount as the mining industry navigates modern resource extraction demands.
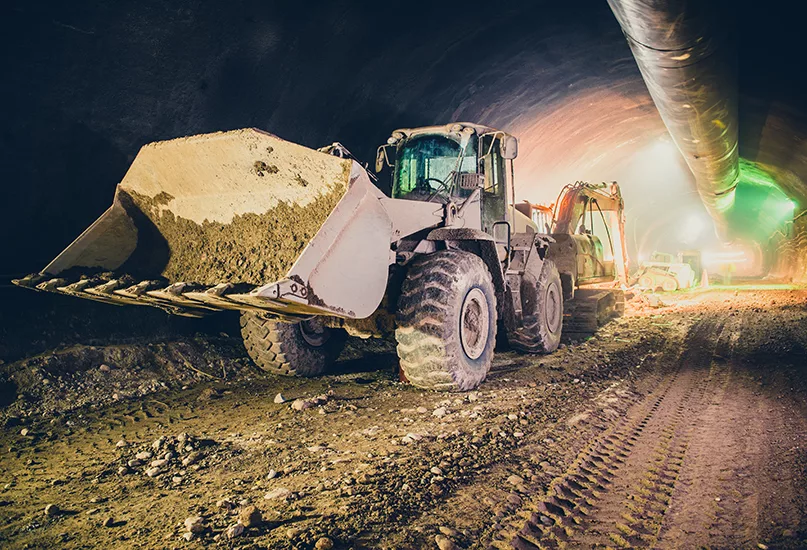
STRIKING A BALANCE BETWEEN SUPPLY AND DEMAND
To prepare for the electrification of equipment and processes, mines must manage the changing balance of electricity supply and demand. To achieve this, mining companies should plan and schedule their electricity supply and demand in a way that supports the entire management system.
On the demand side, as mines transform assets and processes, the challenge becomes more closely linked to energy management, specifically how to manage the new loads to ensure system stability and manage the change in electrical infrastructure while considering that equipment will be powered by electricity.
This requires integrating advanced energy management systems to monitor and optimise energy use, aligning all operations with the available power capacity. Employing digital tools such as real-time monitoring, predictive analysis, and smart grid technologies will permit mines to forecast energy needs more effectively and adjust their operations proactively rather than reactively. This will help mines avoid disruptions and maximise local renewable production for fuel operations.
Increased pressure on electrical grids will need to be offset by on-site power generation and outsourcing power from various suppliers across wind, geothermal, and solar. Mining organisations can alleviate the impact of potentially doubling their electricity demand by investing in microgrids and energy storage that allow them to store excess power and smooth fluctuations in supply, improving energy security, permitting mines to control their costs, and reducing their carbon footprint.
Many companies have started to invest in on-site renewable projects for greater energy independence, driven by the need for reliable, cost-effective, and sustainable energy sources. For example, Rio Tinto’s Weipa bauxite mine in Queensland, Australia, has incorporated a solar plant to supply electricity to its operations, reducing its reliance on diesel generators to lower carbon emissions.
By electrifying mines efficiently and adopting alternative energy resources into the process, we can make mines more resilient and ensure that energy does not become a weak part of the value chain.
BRINGING POWER AND PROCESSES TOGETHER
The mining sector strives to reduce its carbon footprint by integrating electrified processes to replace conventional diesel-powered equipment. Those electrified processes are suitable to reduce energy consumption when new levels of algorithms for control are deployed, leveraging new sensor technologies such as the Internet of Things (IoT), cameras, or artificial intelligence (AI); that new level of automation is an excellent example of how power and process integrations enable new ways to reduce emissions. Not only will this address environmental concerns, but it will also yield substantial operational benefits.
Yet, an electrified mining landscape poses many challenges, particularly in redesigning the electrical infrastructure tailored to suit each mine’s unique demands. The main question of the power purchase agreement (PPA) centres around how we supply sufficient power to meet the industry’s ambitious goals.
Collaborating with domain experts will enable mining companies to craft bespoke and scalable electrification roadmaps. These trusted partnerships will pave the way for mines to achieve their decarbonisation while enhancing operational efficiency. Strategies that focus on resource allocation and energy needs will guide companies through the delicate steps of the electrification journey, creating an optimistic outlook for a sustainable and efficient future in the mining sector.